Building a Safer and More Efficient Workplace Through Regular Equipment Checks
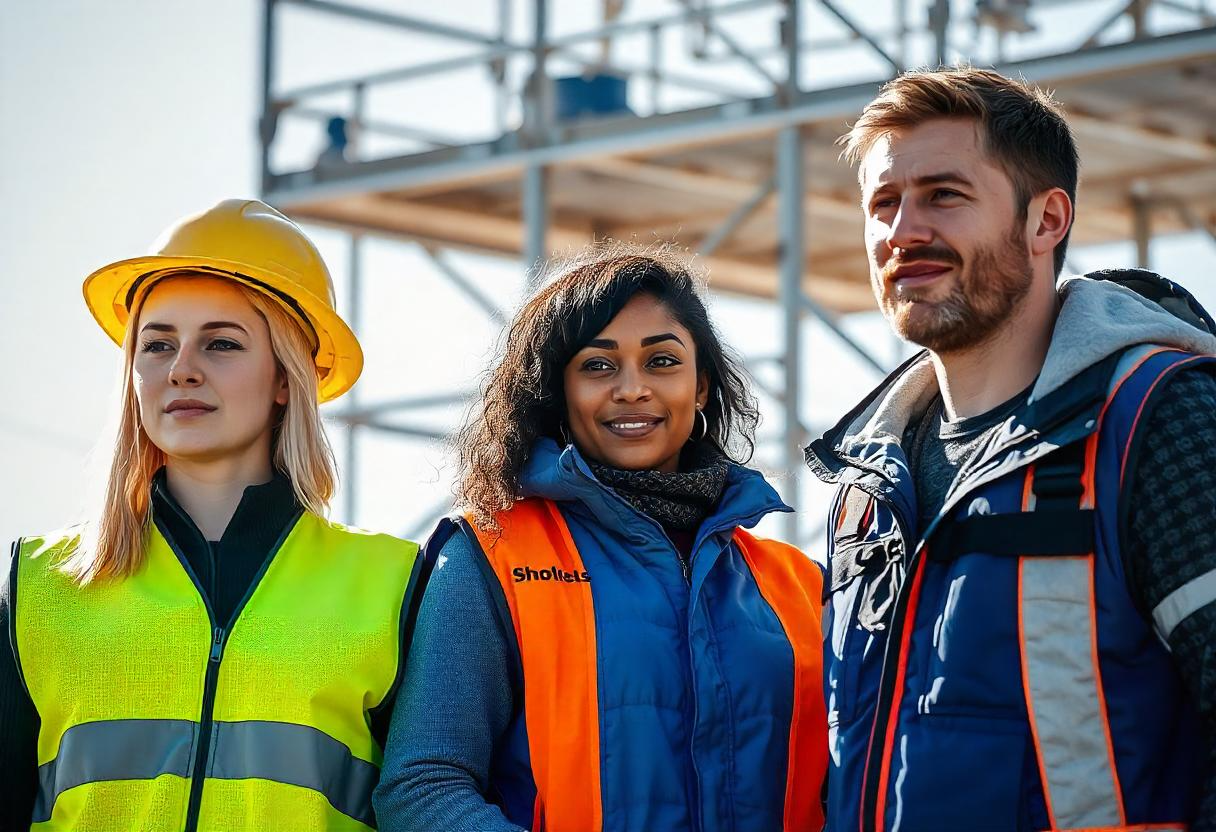
When you walk into a well-organized factory, a busy warehouse, or even a small workshop, you can often feel a sense of order and safety. Everything seems to have its place, and the workers appear confident as they handle their tools and machines. This doesn’t happen by chance. It is the result of careful planning, regular monitoring, and especially frequent inspections of every piece of equipment in use.
Regular equipment checks are not just about keeping machines running smoothly. They play a huge role in preventing accidents, reducing downtime, and creating a work environment where people feel safe and motivated. Many organizations also choose to train their supervisors and safety teams through detailed learning programs like an OSHA 30 Hour Course to understand workplace hazards and ensure compliance with safety standards.
Let’s dive deeper into why regular equipment checks matter, how they can be done effectively, and how they can build trust among your team while saving you money in the long run.
Why Equipment Checks Are Essential in Preventing Hazards
Workplaces are full of moving parts—both literally and figuratively. Machines, electrical systems, tools, and vehicles are constantly in use. Over time, wear and tear can create hidden risks. A bolt might loosen, a cable might fray, or a safety switch might stop working. If these issues are not caught early, they can lead to accidents, injuries, or even major disasters.
An old supervisor once shared a quick story with me: “One day, our conveyor belt stopped suddenly during peak production. We found that a simple roller bearing had worn out, something we could have spotted earlier. Instead, we lost hours of work and had a near miss when the machine jerked unexpectedly.” That small overlooked part could have been caught with routine checks.
Regular inspections are like health check-ups for your machines. Just as people need regular medical tests to catch issues early, your equipment needs ongoing attention. This proactive approach helps in preventing hazards before they become emergencies.
Step-by-Step Guide to Implement Regular Equipment Checks
Many companies know inspections are important, but they struggle with where to start. Here is a practical step-by-step guide to help you implement regular checks in your workplace:
Step 1: Create an Inspection Schedule
Begin by listing all the critical equipment in your workplace. Assign each item a frequency for inspection—some may need daily checks, others weekly or monthly. Post the schedule where everyone can see it. When everyone knows the plan, they are more likely to follow it.
Step 2: Train Your Team
Provide proper training to the people who will be performing the checks. Show them what signs of wear or malfunction to look for. Consider enrolling key staff in structured learning programs that cover workplace hazards, such as courses similar to OSHA Courses Online, so they understand both the technical and legal aspects of safety inspections.
Step 3: Use Checklists
A simple checklist can make a huge difference. Break down each machine into parts—belts, motors, guards, switches—and make sure every point is reviewed. Encourage your team to tick off items as they go. This makes the process systematic and reduces the chance of missing something important.
Step 4: Document Every Check
Always keep a record of inspections. Write down what was checked, what problems were found, and what actions were taken. This not only helps you track the health of your equipment over time but also provides proof of due diligence if there is ever a regulatory audit.
Step 5: Act Immediately on Findings
A checklist means nothing if you don’t fix what you find. If a safety guard is loose or a hose is leaking, address it immediately. Waiting until later often means the problem grows bigger or causes an incident.
How Regular Equipment Checks Boost Efficiency
It’s easy to think of inspections as time-consuming, but they actually save time. Machines that are checked and maintained regularly break down less often. That means fewer emergency stops, fewer repair bills, and more consistent output.
I remember visiting a packaging plant where daily inspections were part of the morning routine. The supervisor told me: “We used to have a breakdown almost every week. Since we started our daily check program, we’ve gone three months without a single major stop.” The confidence in his voice showed how much value they gained from a simple habit.
Building a Culture of Safety
Regular equipment checks do more than protect machines; they protect people. When workers see that management takes the time to check and maintain equipment, they feel valued. They know their safety matters. This leads to a culture where everyone looks out for each other and reports potential problems instead of ignoring them.
Encourage workers to speak up if they notice something unusual—an odd sound, a vibration, or a burning smell. Often, the people using the equipment every day are the first to sense that something is wrong.
How to Convince Your Team and Management
Some people might initially see regular checks as extra work. But you can build support by showing the benefits. Share stories of accidents prevented, or show how much money was saved by catching a problem early. Point out that safety is not only about avoiding injuries but also about running a smooth, efficient operation that everyone can be proud of.
When management understands that inspections help avoid production losses and costly repairs, they are more willing to invest in tools, training, and time for checks. Similarly, workers become motivated when they see fewer breakdowns and a safer environment.
Explore OSHA Courses Online to equip your team with up-to-date practices and compliance insights.
Integrating Technology into Equipment Inspections
Today, technology can make inspections even more effective. Many workplaces use digital checklists on tablets or smartphones. These tools allow instant reporting and photo documentation of issues. Some systems even send reminders when a check is due, so nothing slips through the cracks.
Thermal cameras, vibration sensors, and other advanced tools can detect hidden problems that the naked eye might miss. Investing in such technology can significantly reduce the risk of hazards while improving overall efficiency.
A Final Word on Investing in Safety
In the end, regular equipment checks are not an expense; they are an investment. They protect workers, maintain productivity, and build trust across the organization. When you commit to routine inspections, you send a clear message that safety and efficiency go hand in hand.
If you want to strengthen your team’s knowledge and ensure everyone understands the standards, consider structured learning programs that provide detailed guidance on workplace safety.